In the small town of Jandiala Guru in Punjab, thatheras are hard at work. A community that manufactures brass and copper utensils, they hammered away at their dim future. For this community of workers, manufacturing utensils is not just a form of livelihood; it defines their life. But with the gradual prominence of stainless steel in our daily lives, this traditional craft form seemed to be on a downhill journey into oblivion.
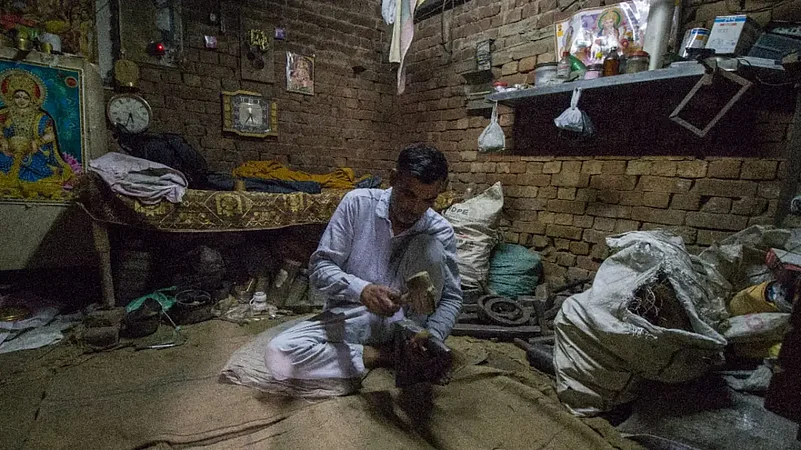
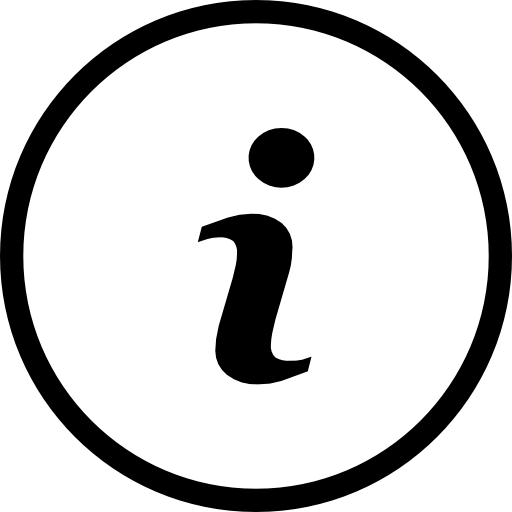
While you and I may not know much about the Thatheras, a group of youngsters are burning the midnight oil to ensure the skills of these metalsmiths survive for their future generations. Started in 2018 under Shri Ram College of Commerce’s Enactus, a student-run international non-profit organisation, Punjab Thathera Art Legacy (P-TAL) is an independent startup that aims to revive this dying art form of hammering brass and copper sheets into traditional utensils.
Life in the Bylanes of Jandiala Guru
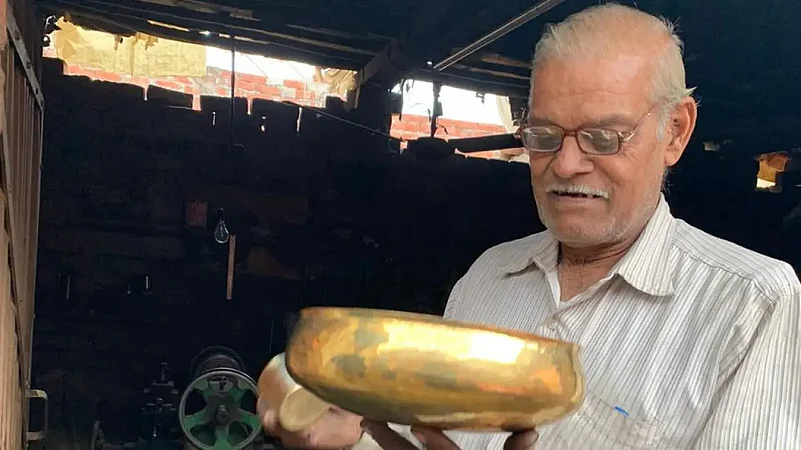
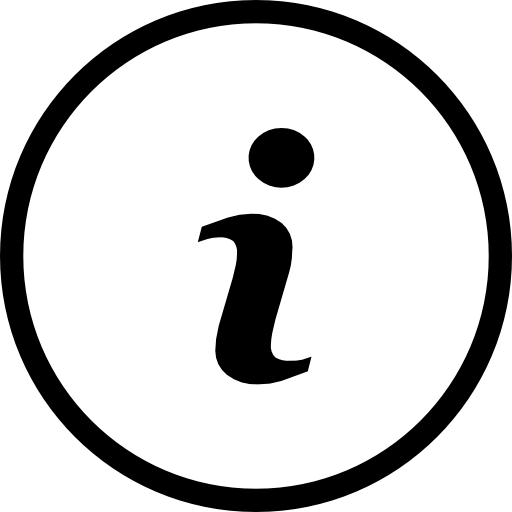
20 kilometres from Amritsar, Punjab’s cultural and religious epicentre, is a craft town. The sound of artisans clanging away at metal sheets forms the symphony of the small bylanes at Jandiala, which was established by Maharaja Ranjit Singh. He brought the most skilled metalsmiths under one roof and over time, their expertise earned them a place as India’s only craft form in the UNESCO Representative List of Intangible Cultural Heritage of Humanity from India, in 2014. But outdated techniques and a dwindling number of practitioners of the craft almost brought thathiyar to the point of no return, standing at the precipice of being delisted from UNESCO, which also believed it had little scope of revival.
Until P-Tal happened.
How it all began
P-TAL started out as one of the projects under Project Virasat by students of Enactus SRCC in 2018. Their aim? Working towards alleviating the problems faced by craftspersons, and creating opportunities not only for the existing artisans but also for their future generations, so that they can safely carry on with the legacy.
“Under Virasat, we researched dying craft forms that needed support and sustenance. We found that this incredible thathiyar art form was faced with an uphill battle. Competition from stainless steel and aluminium utensils was a big challenge. The crafts colony of Jandiala Guru was also exploited by middlemen, often earning as low as Rs 2000 a month for all their hard work, made worse by a decline in demand for copper and brass utensils,” says Aditya Agrawal, co-founder and CEO at P-TAL, who was associated with the initiative from its inception at SRCC.
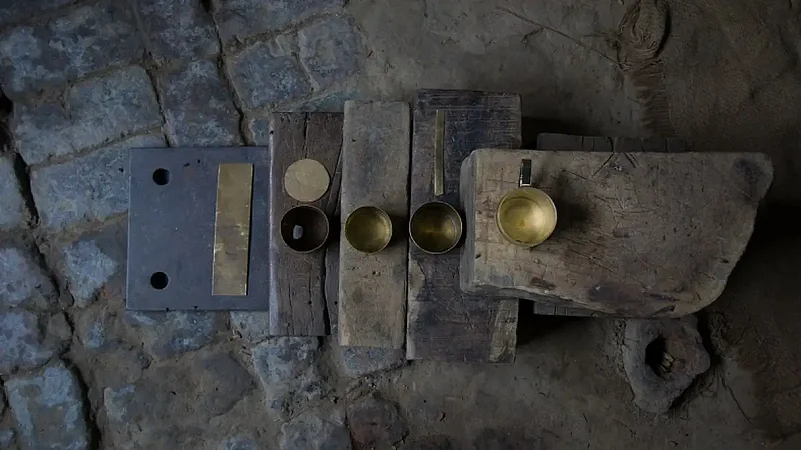
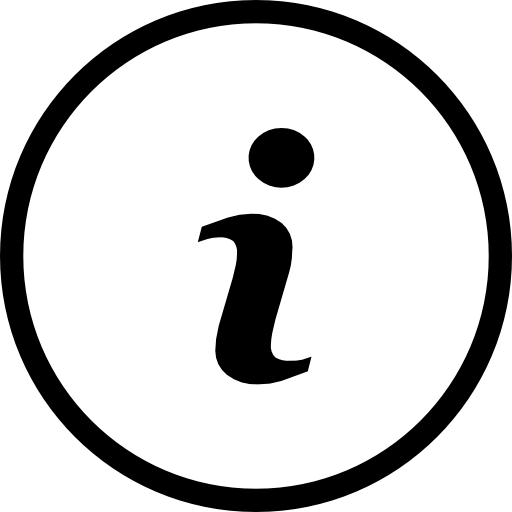
But the going wasn’t easy. In an entire village sceptical of outsiders, Manohar Lal was the first thathera to get onboard P-Tal. Ignoring the naysayers, he invested a small amount in the venture, and his zeal to learn new ways of an old profession soon showed the way to a younger generation that followed suit. P-Tal had started taking shape. Through dedicated efforts, volunteers organised the community of thatheras at Jandiala into a self-help group, which is now an independent startup by the name of P-Tal. A team of 15 odd individuals works to improve their production line, streamline their supply chain and help provide their products access to larger markets and global recognition.
Carving a Better Future
In India, eating in brass and copper vessels has been practised for years. Considered beneficial for health, these vessels are expensive and harder to maintain and have lost the favour of the masses in modern times. P-Tal hopes to change that. Their three-pronged approach includes institutionalisation of artisans, design development and training, and market access through modern techniques.
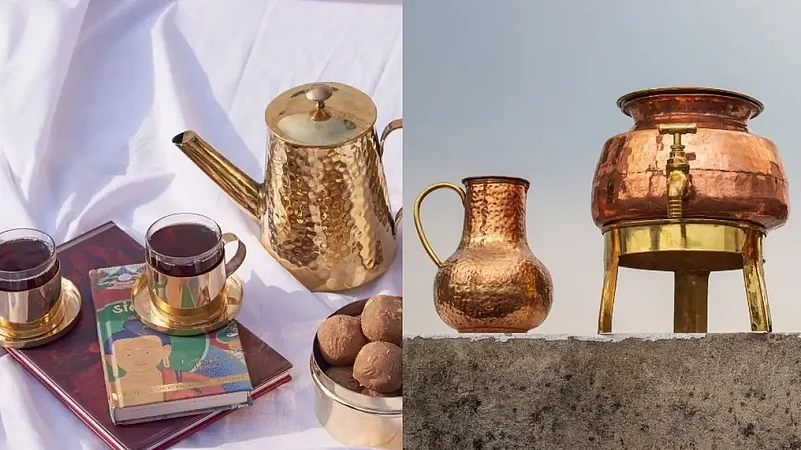
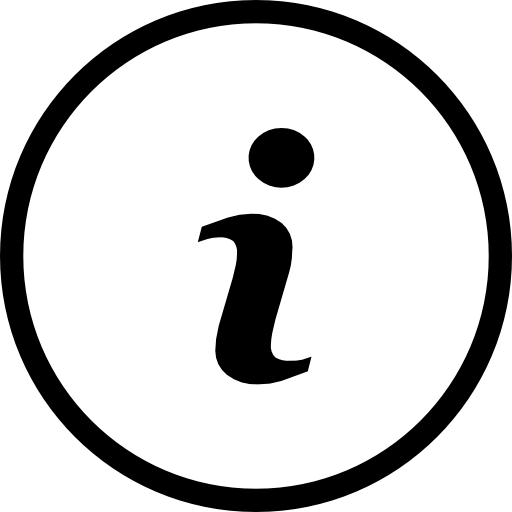
“The craftsmen initially crafted products having outdated designs, we collaborated with professional and veteran designers who came up with 85 new designs catering to niche markets. We ensure strict quality standards for our products,” explains Kirti Goel, co-founder and head designer of P-TAL. With their involvement, artisans started developing small modern use items like teacups, glasses and bowls which had a demand in the market. Along with generating additional revenue for the artisans, it also helped them to make use of wastage that came out of brass sheets which earlier couldn't be put to much use, saving costs and reducing wastage. Earlier, the thatheras were paid Rs 30 for a plate; they now earn Rs 1400 for the same product.
In addition to focusing on utility-based products, the artisan community associated with P-Tal implemented newer designs with a modern touch, while retaining their traditional ingenuity. “For example, we attached a tap along with a lid and a stand to a copper matka or Tamera (a traditional design) to transform it into a water dispenser,” says Aditya. The fusion of brass and copper also enhanced the visual appeal of traditional products.
A Homecoming Amid Covid
P-Tal, which started as a college project, now impacts 55 families of artisans, increasing their monthly incomes by over 600% in the last 3 years. The pandemic, which impacted the revenues of artisans, also brought a ray of hope, of some sort. Many youngsters, who had left the craft and even the town for greener pastures, came home amid the coronavirus lockdown, and back into the cluster of artisans, hard at work. “We now work with 8 young thatheras, who have left their jobs and hope to take their family legacy forward by practising the art form,” Kirti says.
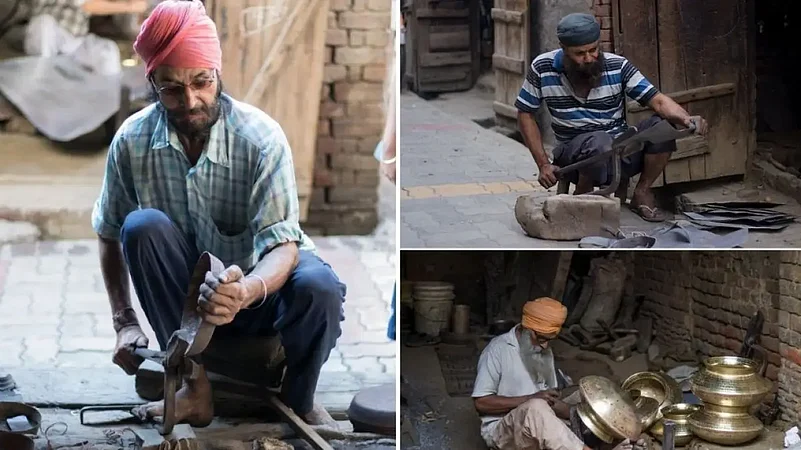
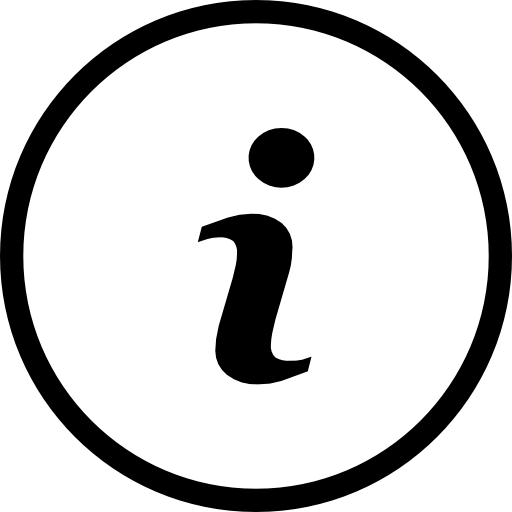
Turning a New Chapter
For the local artisans, one of the biggest benefits of association with P-Tal is access to markets. Pre-covid, most of the revenue came from sales at physical stores and markets. Today, 80% of the revenue is generated through their website and the rest is from marketplaces and social media. While they have miles to go, P-Tal has shown the way to other initiatives that work on grassroots levels. All the revenue that is collected after selling the copper and brass utensils is reinvested into the business, after giving the thatheras their fair share. To some, it may not seem like a lot, but to the small community of artisans toiling away, this gives them a chance at a better life while retaining their heritage. Sometimes, that is all we need.
To help support the thatheras of Jandiala Guru, buy their products at: https://ptal.in/